Regarding the quality of printing materials, these factors should be paid attention to
Published on.
2022-12-07 10:07
Introduction: Printed matter shows its value by imprinting on the surface. Glazing is a processing technology in which a colorless transparent coating is coated on the surface of printed matter and a thin and uniform transparent bright layer is formed on the surface of printed matter after leveling and drying. Glazing can not only enhance the brightness of the printed matter surface, protect the printed text and text, but also will not affect the recycling of paper. This article shares the relevant content of factors affecting the quality of glazing, for the quality supply chain for friends reference:
Glazing
The light is coated (or sprayed, printed) on the surface of the printed matter with a layer of colorless transparent coating, which protects and increases the luster of the printed matter after drying. On the surface of the printed matter coated (or spray, printing) on a layer of colorless transparent coating, after leveling, drying, pressing, curing on the surface of the printed matter to form a thin and uniform transparent bright layer, to enhance the smoothness of the carrier surface, protect the finishing processing function of the printing text, known as the glazing process. Glazing process of printed matter can be divided into coating glazing, coating voltage, UV glazing, pearlescent pigment glazing and so on.
| pictures from baidu picture
01 Glazing suitability
The glazing of printed matter mainly refers to the influence of the printing paper and printing ink. The main influencing factor is the crystallization of paper, ink and printed matter.
1) Paper properties
The glazing quality of printed matter depends on whether the paper has good glazing. Among them, smoothness and absorbency are the main factors that affect the smoothness of paper.
Smoothness of paper
The so-called smoothness, is the surface of the paper smooth uniformity. When the paper smoothness is high, the glazing coating can have good contact with the paper, and smooth on the paper, after drying can form a higher smoothness film surface, has a good glazing effect; When the paper smoothness is low, because the paper surface is rough and the flatness is poor, the paper will absorb the glazing coating, so the glazing effect is not good. In view of this deficiency, a layer of substrate should be coated on the surface of the printed matter before glazing.
Absorptive property of paper
The so-called absorption performance, as the name implies, is the paper absorption ink connection material and solvent performance. The capillary absorbency and porosity of paper fiber determine whether the surface of paper has strong absorbency. When the paper has strong absorption, it will increase the viscosity of the coating. Thus reducing the leveling property; On the contrary, when the absorption performance of the paper is weak, then the glazing coating viscosity will not increase due to drying. This makes the solidification, penetration and conjunctiva performance decline, it is difficult to form a good film on the surface of the printed matter. To solve this problem, we should extend the leveling time and increase the drying temperature to improve the glazing quality.
2) ink performance
In terms of ink performance, the main factors that affect the quality of printing ink are the wetting effect and the granularity of ink. When the particles are small and the dispersion is high, due to the effect of coating pressure, it not only has good leveling, but also has a higher smoothness of the film layer. On the contrary, when the particles are large and the spread is poor, it will increase the roughness of the surface of the ink layer. Therefore, when choosing the ink, we should ensure that the ink has good alcohol resistance, acid and alkali resistance, solvent resistance, heat resistance and other characteristics, which can prevent the change of text and text, but also prevent the appearance of wrinkle. In addition, in order to prevent the discoloration of ink, it should be ensured that it has strong adhesion and gloss
3) Crystallization of printed matter
The main reason for the crystallization of printed matter is that the printed matter is used for too long, or the excess of the background ink is added, which leads to the crystallization of the ink film on the surface of the paper, and then leads to the adhesion performance of the coating and the ink layer is reduced, and finally the quality problems such as "pitting" and "color face".
To solve this problem, the usual way is to add lactic acid (5%) into the glazing paint and stir evenly to glazing.
02 Coating properties
Under normal circumstances, coating viscosity, surface tension and volatility will affect the quality of printing. From the point of view of the viscosity of the coating, its viscosity value is too large or small can lead to the printing surface coating imbalance, thus affecting the glazing quality. Because the surface condition of the printed matter that needs to be coated is often different, the viscosity value is also different, which needs to determine the viscosity value of the coating from the viscosity change of the coating, drying and pressing, so as to ensure the adaptability of the viscosity value of the different process of glazing. From the point of view of the surface tension of coatings, the surface tension value is not the same because of the different types of coatings, so the wetting, penetration, adhesion and film forming effect of coating after coating are not the same. The size of the surface tension of the coating is inversely proportional to the difficulty of the printing surface wetting. The smaller the surface tension is, the film surface formed by the coating leveling is more uniform and smooth. On the contrary, if the surface tension of the coating is larger than the surface tension of the printing film, then the surface of the coated printing matter will not only shrink, but also form trachoma in the local area.
From the volatile coating solvent point of view, because of the different coating formulation, then the coating solvent type, proportion and coating and drying evaporation rate are not the same. In particular, the rate of solvent volatilization is closely related to its own properties, but also to many factors such as air humidity and its flow and the size of the ambient temperature and air contact surface. Too fast solvent volatilization rate will reduce the leveling of paint, and there are streaking, trachoma and other quality defects, and even cause moisture condensation, glazing film dry will appear black or even cracking phenomenon; Paint volatilization rate is too slow affect paint drying, and conjunctival hardening is blocked and stain resistance is poor. In view of the above shortcomings, we should reduce the coating rate and increase the baking temperature respectively. From the above analysis, the selection of printed matter glazing coating, should adhere to the principle of scientific and practical, economic and reasonable, and combined with the printing matter's own glazing suitability, coating performance, technology, drying rate and coating environment and other factors, scientific and reasonable selection of printed matter coating
03 Coating process
In the coating process, there are three factors affecting the quality of printing material: coating quantity, drying conditions and coating rate.
From the point of view of coating quantity, the gap between coating roller and measuring roller is mainly used to adjust the size of coating quantity. Whether the gap between two rollers is reasonable or not has a direct influence on the uniformity, surface gloss and smoothness of the coating. Therefore, when glazing, the actual absorption performance of the substrate must be combined to adjust the price and determine the size of the coating amount. From the point of view of drying conditions and coating rate, the drying time and the required temperature form the drying conditions, and the drying conditions should be determined from the type of coating, coating rate, coating amount and the surface properties of the printed matter. For example, on the basis of ensuring a reasonable coating, if the coating rate is faster, it will shorten the contact time between the substrate and the coating roller, the absorption of glazing coating will also reduce, and then reduce the brightness of glazing.
04 Equipment
The equipment has a serious impact on the glazing quality of printed matter from time to time, and even leads to the phenomenon of direct scrap of printed matter, which not only wastes resources, especially improves the production cost of enterprises, but also affects the economic benefits of enterprises.
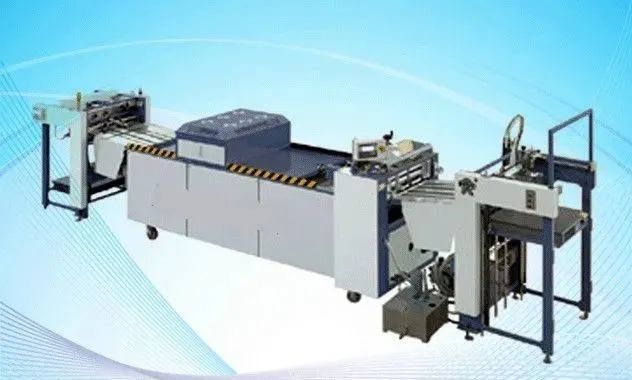
Therefore, enterprises should not only strengthen the professional skills training of operators in the use of equipment, but also improve the professional and technical level of operators. They should also choose equipment according to the actual situation of enterprises. This is because of different printing materials, products, processes and different quality grades and environmental protection needs, the selection of equipment is not the same. On the basis of considering the above factors combined with the economic strength of the enterprise, the existing configuration and the actual situation of product processing, in order to ensure the glazing quality of the premise as far as possible scientific and reasonable introduction of glazing equipment, in order to reduce the production cost of the enterprise, and in the use of equipment as far as possible to control its impact on the quality of printed matter glazing, especially the control of small links.
For example, before coating the printed matter, the calibration work of glazing, coating and other equipment is often ignored. As the operation of the machine leads to the possibility of wear, eccentricity and even bending of the roller body, the sleeve and shaft head of the roller jump due to loosening and wear, etc., and these will lead to the stability of the gap between the "two rollers", and then lead to the coating imbalance in the glazing process, which has a direct impact on the glazing quality.
The content of this article is from Baidu Wenku if there is any infringement, please contact us to delete if you need to reprint, please indicate the source
Featured News